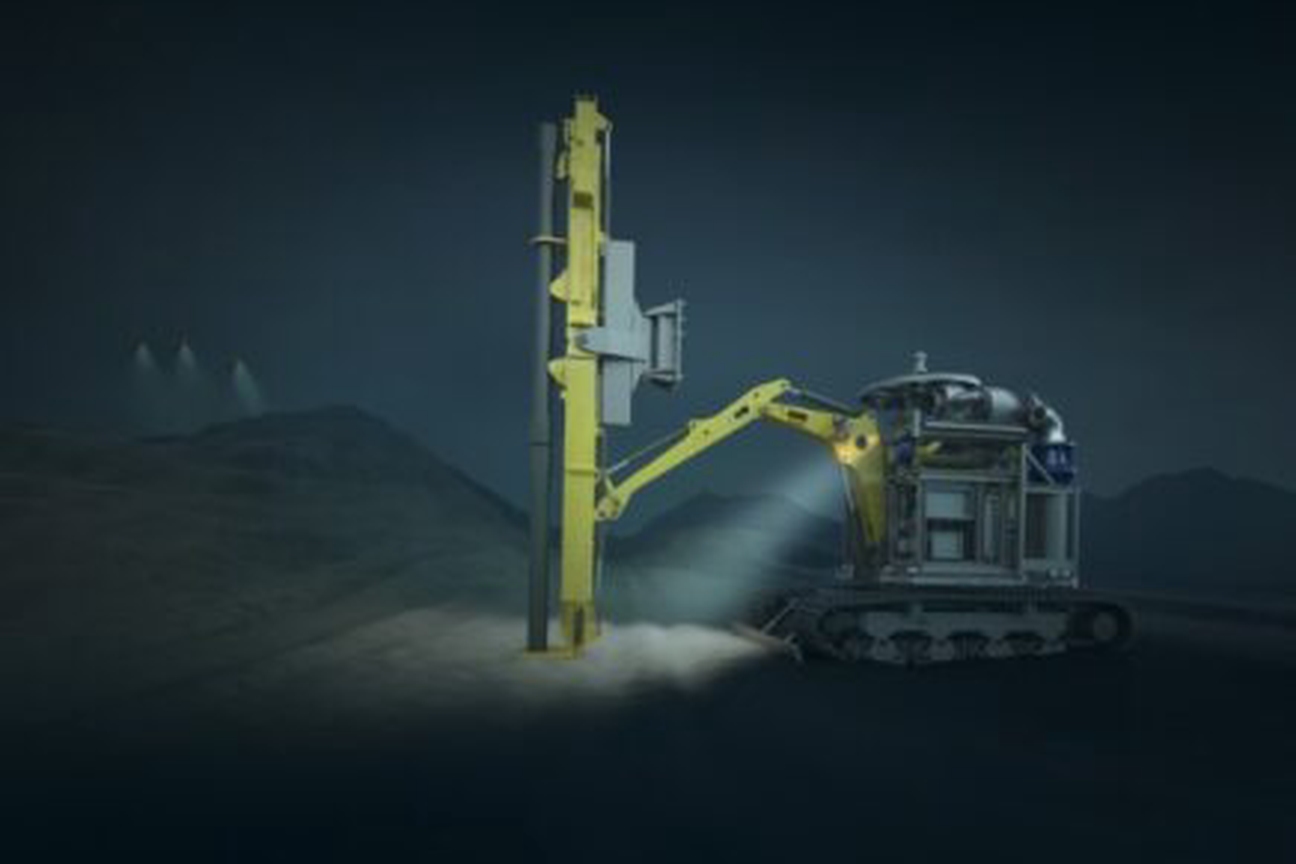
DeepOcean FlexiCore
The FlexiCore technology will be able to obtain an increased number of high-quality cores in less time and with lower costs than conventional methods. The system has so far been used to retrieve seabed cores at water depths of over 1,000m. Our initial plans for commercial utilization focus on seabed mining exploration campaigns and renewable energy developments.
Subsea Geotechnical Survey Solutions
Contemporary marine drilling operations fall into two major categories: ship-based and seafloor based. Ship-based drilling operations involve high operational costs and significant vessel requirements, limiting the pool of available platforms and requiring resource-intensive operations. Seafloor-based core drilling systems can be subdivided into stand-alone robotic seafloor systems or ROV based systems. Options for the latter currently suffer from slow drilling rates and poor penetration. Robotic drills are fully automated but typically require a level seafloor, intricate robotic systems, and surface vessel repositioning between each drill site. This is the case even for closely spaced stations or re-attempts on site.
Further challenges associated with these methods are that they cannot collect samples at sufficient depths (especially for seabed mining operations) and are not flexible enough to take samples from both unconsolidated loose sediments (typically using coring equipment based on weight/piston) and hard rocks or solid consolidated deposits (using rotary drilling equipment with core bits). They’re also unable to concurrently collect geophysical and drilling plume information.
Equipment that can drill to the desired depths and make the large numbers of boreholes required by clients are currently based on drilling vessels/platforms. These methods can prove too expensive for some applications, such as marine mineral exploration. Alternatively, seabed drilling towers provide all the drilling equipment to the seabed but are inflexible; they have less mobility; must be resting on a near-horizontal seabed to drill; and must be fully automated. This can result in frequent mechanical issues requiring the recovery of all equipment to the support vessel.
The FlexiCore System
FlexiCore combines a marinised land-based coring system (in which certain equipment components have been replaced), mounted on an existing subsea crawling vehicle.
The key subsea coring challenges which FlexiCore is designed to tackle are:
• Coring in variable substrate, including sediment and rock
• Core drilling in varied lithology
• Operation in sloped terrain, and at various core drilling angles to the seafloor
• Being deployable from an industry-standard offshore support (subsea) vessel or scientific research ship
• Being capable of changing drilling bits at the seabed
• Quick transition from one coring site to another, even in sloped terrain, without the need for system recovery
• Recovery of more than 30m of core per day from multiple field sites
• Recovery of over 50% of the core material (with the goal of over 95%)
• Being able to drill to a depth of more than 200m below the seabed
• Potential use in multi-day core drilling operations for site geophysical and environmental characterization
• Additionally, the FlexiCore support setup should allow concurrent collection of geophysical data and monitoring of any drilling plume
The FlexiCore system is designed to meet these operational criteria through the innovative application of established offshore and onshore technology.
FlexiCore is mounted on the Seabed Excavator, which is based on a Perry Slingsby XLX ROV system that was built in 2009 and has been used for various special salvage projects worldwide.
It has achieved a maximum dive depth of 3,200m, and holds a record for continuous working time up to seven days. FlexiCore is rated to 4,000m depth, and is deployable from any ROV-capable subsea vessel with sufficient crane capacity.
Moreover, the Seabed Excavator is proven to operate in up to 30° slope, in variable terrain, and is coupled with a bespoke marinised and modified Epiroc drilling system. This is capable of drilling at any angle to allow operation in challenging terrain and drilling angle environments.
The FlexiCore system can be operated in conjunction with a conventional work-class ROV, providing a theoretically limitless supply of coring components.
This also enables retrieval of cored material to the support vessel for near real-time assessment and decision making.
The support ROV’s role facilitates the system’s operational responsiveness to variable lithology. It allows a wide range of in field-swappable drilling bits and core lifting systems to be rapidly exchanged on the seafloor.
In line with this, several variations of drill bits are prepared in a subsea basket, allowing for quick swapping without the need to recover the FlexiCore system. Additionally, using an ROV to recover core samples to a vessel without interrupting drilling operations, enables continuous drilling, and variations to coring operation on-the-fly as a result of ongoing assessment of the ore body collected.
One in-house innovation which enables the system to work more effectively in harsh offshore conditions, is the development of a high-power hot stab.
This allows the FlexiCore umbilical to be disconnected or reconnected on the seabed and can increase the weather window for operation: up to 4.5m SWH.
Use of the hot stab enables coring operations to be paused and resumed without recovery and re-deployment of the FlexiCore system.
This combination of adaptable drilling angle, field-swappable drill bits, and detailed drill control (i.e., real-time user-controlled drilling speed, bit pressure, and water pressure) is intended to enable exceptional core recovery in variable lithologies, from soft sediment to highly resilient jasper.
Marinization and Initial Wet Testing
Prior to deploying FlexiCore from a vessel offshore, system development, construction, and initial testing were completed. Initial trials involved an on-land test and an in-water (pier-side) test. The system was tested twice from a quay side. The second test involved a complete system integration, in which an operational test including ROV deployment occurred. Successful completion of these trials indicated the system was fully qualified for its subsequent first operational deep-water deployment at the Mohns Ridge, a remote and challenging field environment.
As part of the initial trials, the FlexiCore system was extensively tested in progressively more complex testing scenarios. This culminated in a dry run field test with full mobilisation in a pier-side trial, including full operation of the integrated drilling system. This stepwise approach to system testing aims to minimize the risk of system failure by stressing all points of failure in a controlled environment. It has also provided opportunities to train both vehicle and ship operators in equipment operation prior to working in a remote field site.
During the in-water trials, a combined length of approximately 12m of seabed cores were recovered, with a recovery rate of up to 80%.
The trials involved testing the operation of all system functionality, and full integration with an ROV in relation to logistics and handling of rods and cores between FlexiCore and the storage basket.
The wet test was performed at 25m water depth, where the system drilled/cored in various types of bedrock.
Throughout these trials several clients visited the test site and were able to monitor the wet tests and coring operations in real-time from the quayside. The trials also provided an opportunity to verify capabilities for changing drill bits subsea.
The ability to drill, then stop and recover the drill bit to the ROV/basket, then swap for a new drill bit, before continuing to drill in same hole was successfully demonstrated.
Offshore Field Trials
For its first deep water, offshore field trial, FlexiCore was tested within a research campaign led by the University of Bergen (UiB) Centre for Deep Sea Research, at the Mohns Ridge, in May 2023.
This campaign, aboard DeepOcean’s vessel Dina Star aimed to map and further develop knowledge about the geology in the extended Mohns Ridge region of the Norwegian Continental Shelf (NCS). During this field deployment, the FlexiCore system was challenged to work in multiple lithologies with sites chosen by UiB.
At Mohns Ridge the FlexiCore system was tested in extreme conditions (in terms of depth, temperature, remoteness). Priceless experience was gained during the expedition, and this is now being used to improve the system’s capabilities. Resolving the system’s performance along the Mohns Ridge was a significant challenge; all previous drilling operations there have encountered substantial difficulties and achieved at best 20% core recovery of 20m or less of core.
The four main challenges posed during these field tests were the remoteness of the location, geologic complexity of the operation sites, integration of multiple data sources, and the variable down-bore lithology. Despite this FlexiCore achieved high recovery rates on sites where water depths exceeded 1,000m.
Throughout the trials completed so far (during the research expedition and quay side testing), FlexiCore has been able to achieve drilling rates of 20m core per 24 hours. During drilling operations on the Mohns Ridge, we were also able to complete simultaneous operations (SIMOPS), enabling comprehensive environmental baseline data and seismic data to be acquired.
Commercialization
Following the first operational deployment of FlexiCore, we are now preparing the system for deployment within commercial projects.
We plan to utilise FlexiCore to enable rapid classification and quantification of seabed geology, both for sustainable marine mineral exploration, and for sub-seabed investigations required for the installation of marine renewable energy systems.
The potential market for this system is wide. Core drilling, data acquisition, and detailed mapping are all considered important for offshore wind infrastructure, bridge foundations, evaluation of the ground over underwater tunnels, and general seabed related research.
Therefore, FlexiCore is ideally suited to work scopes relating to inter-alia geotechnical assignments, site surveys, and anchoring of wind turbines or other installations.
The demand for a next generation seabed coring solution such as FlexiCore is well established; research institutions and industrial actors in Norway and elsewhere are demanding improved subsurface understanding, beyond what is possible using currently available technologies.
In addressing this requirement, the consortium rolling out FlexiCore are looking to incorporate the system within a diversified exploration toolbox, SIMOPS solution, providing a suite of multi-geophysics and environmental data collection tools.