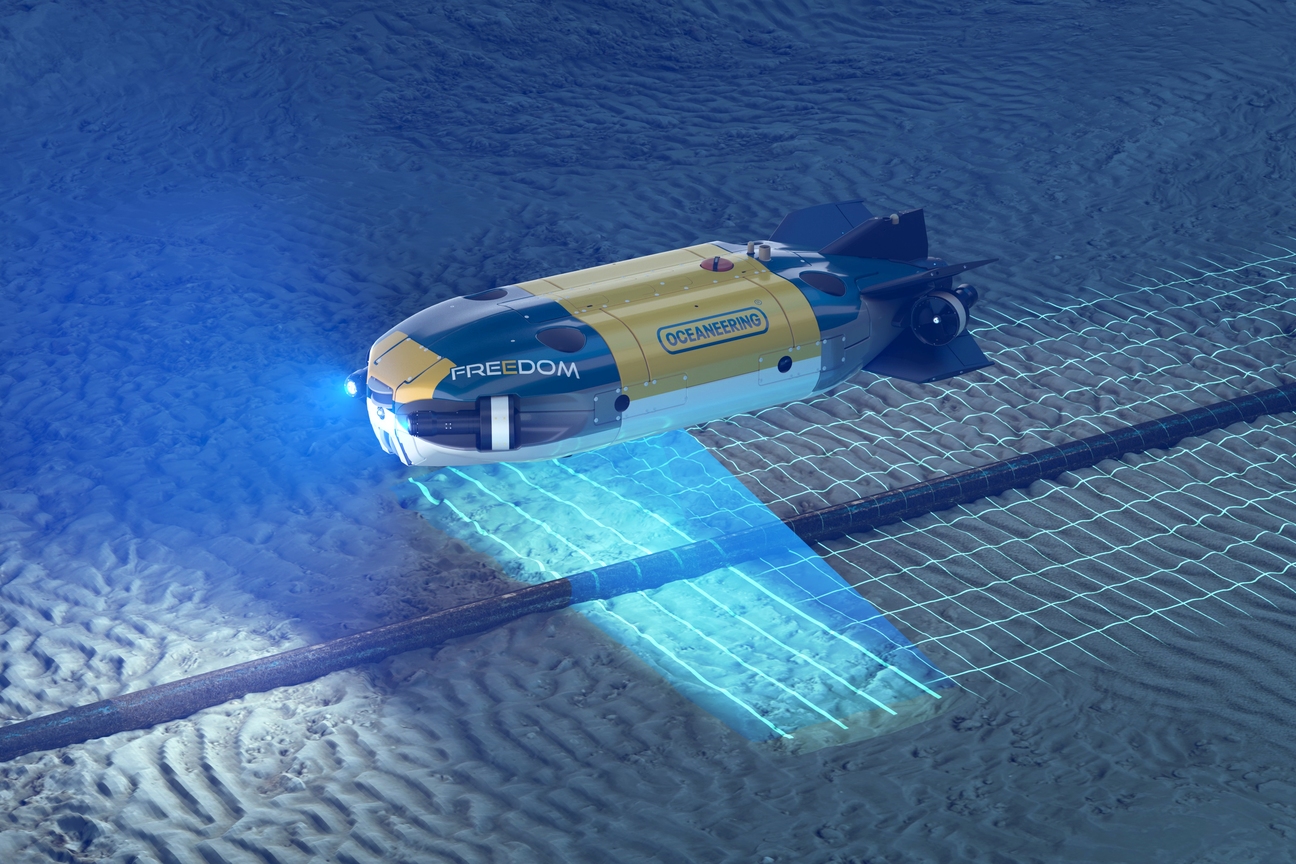
Hybrid AUV/ROV extends the reach of traditional support services
Conceptualizing such a vehicle required engineers to think differently about design to develop a vehicle that would not only enable effective and efficient pipeline inspection services but that could be modified for other applications.
Designing in modularity
Oceaneering’s Freedom AUV/ROV is designed with modular components and standardized, system-agnostic interfaces that allow a range of sensors and tools to be simply plugged in and activated.
The company brought to bear 30 years of experience designing all-electric vehicles and associated components to develop the modular design. One of the keys of the vehicle’s modularity is the use of a common interface that enables plug-and-play connection for sensors, batteries, thrusters, and the intelligent power and ethernet module (iPEM), a fully managed Ethernet switch capable of switching up to 10 Gbps fiber comms with all ancillary channels up to 1 Gbps. The AUV/ROV vehicle also has a single, common cable design that simplifies interconnectivity.
These design elements make configuration—and reconfiguration—straightforward, so the vehicle can be fitted with appropriate modules for a given program. Modularity also reduces construction cost, decreases maintenance time, improves reliability and increases the vehicle’s operational life. The elements that constitute the designs are being futureproofed so they will be usable on future ROV and AUV systems.
Testing deployment readiness
The designers knew the modular concept was promising, but it had to be field tested and proven to demonstrate its capabilities in order for the industry to be confident that the AUV/ROV vehicle could perform as expected.
Testing of the hardware components and the basic software framework began in 2018 using a development vehicle that was tethered and operated under direct human control. Using a development vehicle made it possible for small elements of autonomy to be tested as new components were conceptualized, developed and integrated on the vehicle. This testing approach accelerated system development, enabling rapid progression from TRL2 through TRL3.
Using the Freedom #1 test vehicle, field trials continued, for both hardware and software, initially with the vehicle tethered. This phase of testing took the hardware and software through TRL4.
At this point, the methods for assessing and quantifying performance required a different approach. Over the next four years, the team carried out a controlled testing program that yielded a progressive record of performance improvement, demonstrating the vehicle’s capabilities as it evolved. During this phase of testing, the Freedom AUV/ROV underwent more than 611 days of testing and more than 656 pipeline runs, which includes 65 days of offshore testing.
The TRL process was streamlined in part because of the testing carried out in Tau, Norway, at Oceaneering’s quayside “living lab” facility with workshops, meeting rooms, shoreside cranes, and subsea playground. The vehicle was launched and controlled from the quayside and underwent testing that encompassed navigating shoreside obstacles, including a subsea docking station, pipelines of various diameters, and infrastructure designed to replicate an offshore environment. Components like software, sensors, and batteries underwent rigorous in-water testing at the living lab to not only meet, but surpass TRL 6 requirements for pipeline survey and inspection.
Pushing the envelope
The Freedom AUV/ROV can carry out traditional ROV operations or work in an autonomous and tetherless AUV configuration, with a working range of 120 km, a working depth rating of 6000 msw, and a top speed of 3 m/s. The vehicle is suitably robust and reliable to be deployed subsea for up to six months.
Additional hardware modifications are planned to expand the breadth of the vehicle’s capabilities to include cleaning operations, light intervention, and taking cathodic protection readings, for which field trials are now underway.