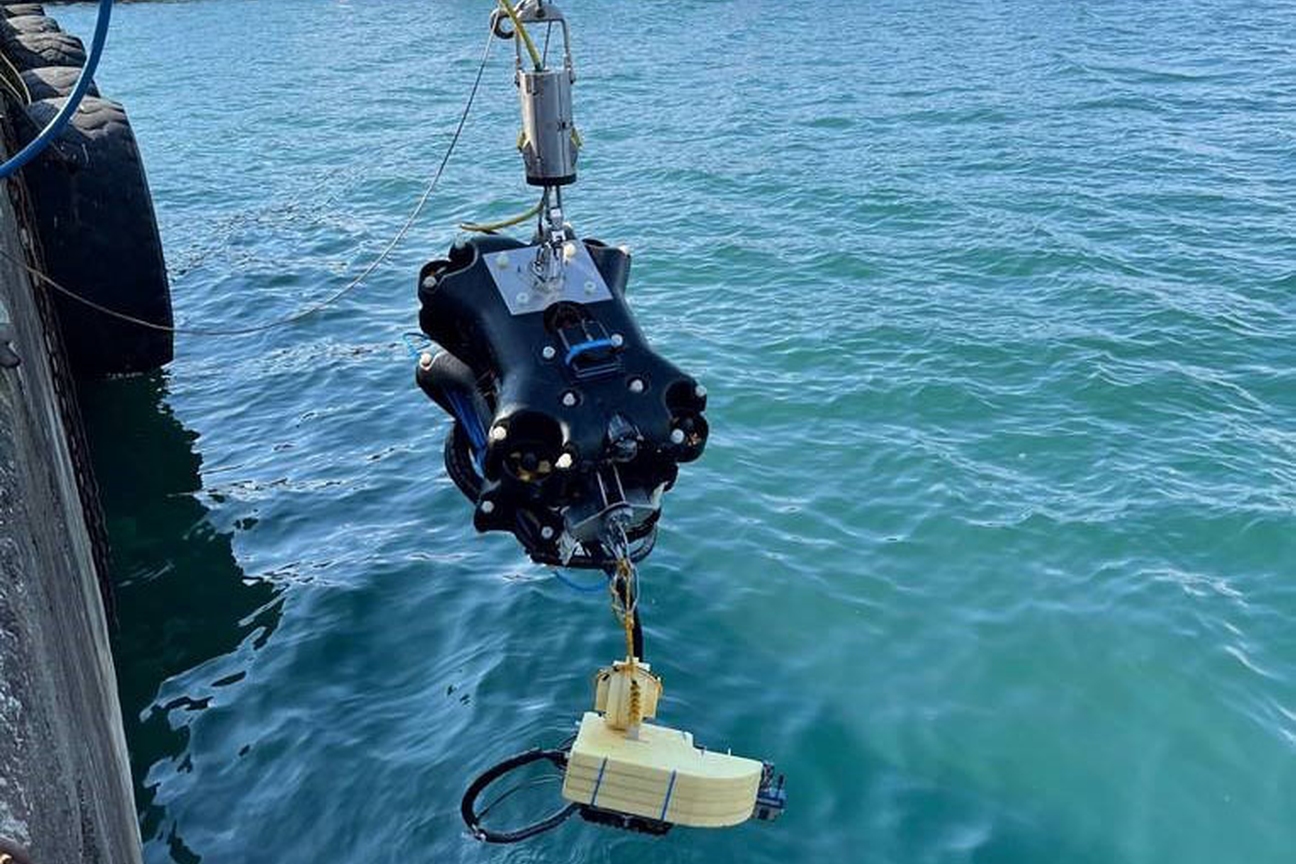
Mini-ARROV cutting the cost and footprint
There is a lot of it to be done and it typically involves the use of work class remotely operated vehicles (WC ROVs). That means the use of a fully crewed support vessel, with up to 15 ROV and six ACFM crew, as well as a project manager, inspectors, and client representatives. Operator Repsol Norge wanted to radically reduce the overheads of this type of work. It contracted Stinger Technology AS to perform underwater weld inspections on the subsea brace-to-leg and brace-to-caisson connection welds at the Yme production facility in the Norwegian North Sea.
Minimal staff offshore and no support vessel
The challenge was to carry out this procedure remotely, using a mini-ROV, with minimal staff offshore and no support vessel. We initially thought this was an almost impossible challenge, due to the complexities of the operation and the equipment involved. Then the Coronavirus pandemic saw a severe restriction on personnel movement, including 14-day quarantine requirements. There was also limited bed space availability on the Yme platform, as it was in the commissioning phase. A radical approach was needed. Stinger’s challenge was to deploy this complex ACFM technology using a deck deployed mini-ROV, with only two staff offshore and navigation and control from onshore.
Small, but powerful
To complete the task, Stinger contracted ACFM specialist TSC Subsea. TSC’s ACFM MagCrawler, a magnetic crawler, is typically deployed by a WC ROV. Instead, Stinger adapted the technology so that it could be deployed by its mini-ROV and so that both could be remotely operated from onshore. Stinger’s mini-ROV is designed to be small enough to be manual handled overboard, but also very powerful, with communications bandwidth capable of integrating other systems, such as crawlers, tooling and even other drones. In this project we washed with 800 bar.
Six degrees of freedom
The standard mini-ROV, which works down to +500 m water depth, weighs only 25 kg and measures 750 mm x 550 mm x 300 mm, but houses eight thrusters giving it six degrees of freedom, eight 1500 lumen LED lights and high-resolution HD 1080 digital camera. The mini-ROV can carry a wide range of tooling, but some adaptions were required to integrate TSC’s MagCrawler, which houses ACFM U31RD equipment, so that it could be conveyed to, and then controlled at, the worksite. We reduced the weight of the MagCrawler and developed and integrated a remotely activated release hook onto the mini-ARROV, so that it could carry and then release the MagCrawler. The MagCrawler’s controls bottle was also integrated onto the mini-ROV, almost doubling its size. The vehicle was then successfully used to deploy, view and control, via a tether, the MagCrawler.
Two technicians offshore
Only two technicians were deployed offshore, one from TSC and one from Stinger, to carry out launch and recovery and ensure all tooling remained operational. While the initial plan was to have the MagCrawler and mini-ROV pilots working side by side in Stavanger, the operation was completed with them working separately in the UK and Stavanger. Both teams successfully worked together via a Teams video meeting, alongside specialist inspectors based at locations in Stavanger and the UK, as well as company representatives. The project was a significant step forward for performing ACFM inspection. However, it also proves that other complex tasks normally performed using WC ROVs can be done using deck launched mini-ROVs and with limited personnel offshore. Additionally, it shows that other systems, currently deployed using work class ROVs and reliant on vessels and vessel availability, could also be deployed and operated with minimal offshore crew and no vessel.
New apporach
It also demonstrates that operators with a vision like Repsol can challenge the supply chain to take a new approach, resulting in vastly lower CO2 emissions and cost, simplifying logistics, and reducing demands on bed space and vessel availability.
– Despite an inspection duration measured in months not weeks, the Inspirer mini-ROV operations delivered on the required inspection quality, resulting in fewer offshore man days than a comparable IMR vessel campaign. Stinger/TSC’s improvements to workability, implemented during the Campaign, have potential to reduce costs by a factor of 10 (90%) or more. Further, Repsol’s decision to install a high-capacity fibre optic datalink at Yme, enabled this remote onshore working/telepresence that resulted in benefits for safety, reduced exposure to helicopters, and an environmental reduction of CO2, says Roland Daly, Delivery Lead Subsea, Repsol Norge AS.