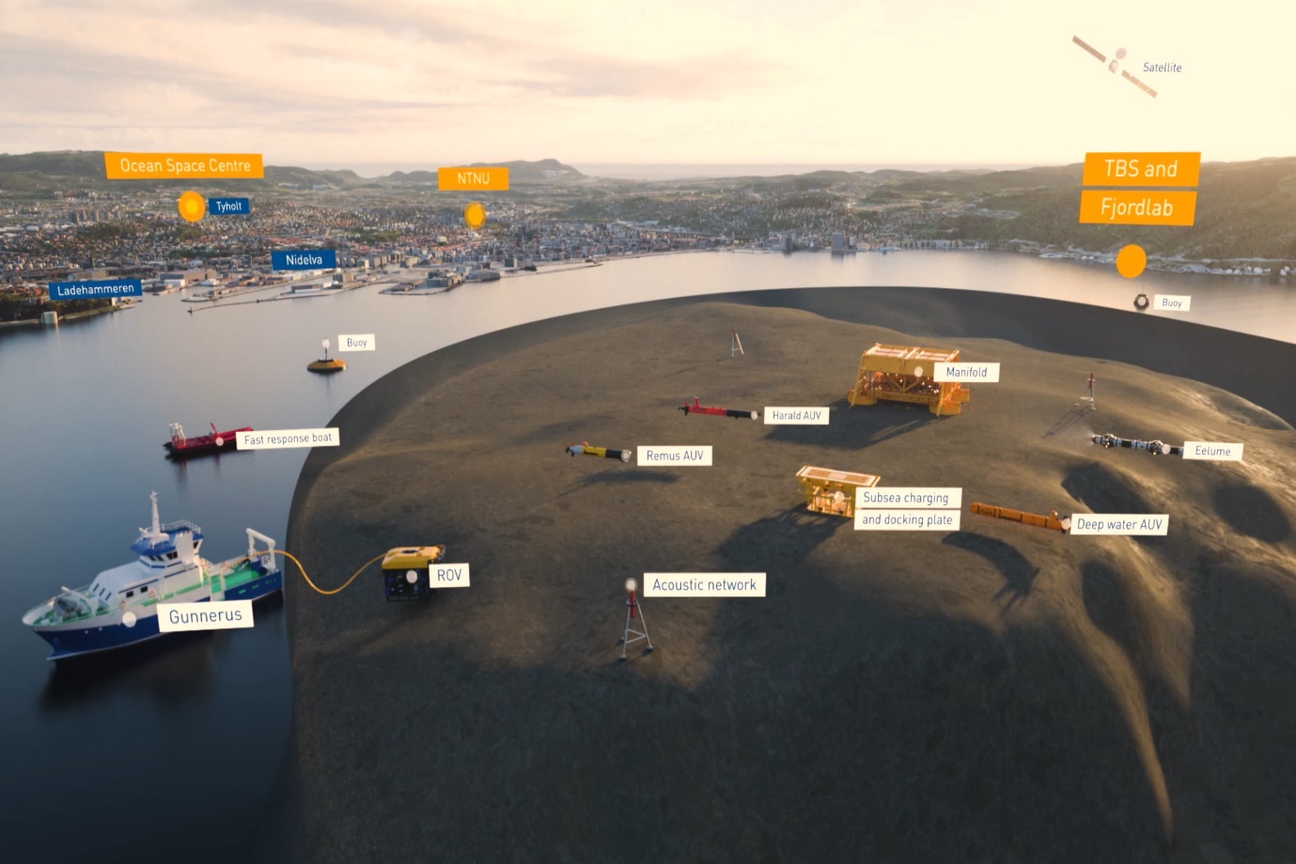
OceanLab - full scale subsea testing and validation facility
NTNU’s Applied Underwater Robotics Lab (AUR-Lab) has been developing a full-scale subsea testing and validation facility in Mid-Norway in the Trondheim fjord since 2017. These activities are the result of NTNU’s long-term collaboration with Equinor that is related to the development of a test and validation site for underwater technology, including the autonomous/resident vehicles and underwater intervention drones (UIDs).
The testing and validation facility has continued to be further developed as part of the joint SINTEF and NTNU OceanLab project financed by the Research Council of Norway. OceanLab aims to establish full-scale laboratories to meet the requirements for education, research and innovation in marine and maritime sectors.
Apart from subsea facilities, the OceanLab covers a test area for autonomous ships, an aquaculture field lab, two oceanographic buoys and communication infrastructure. The whole test site has been named the OceanLab. The test site is expanded to include the shoreside control room that is linked to the subsea infrastructure allowing testing and operation of subsea assets from the control room and/or monitoring from any remote location.
The test site
Currently, NTNU operates the OceanLab subsea infrastructure distributed at two seabed locations 2.2 km apart. In 2017, the Pig Loop Module (PLM) was installed at location B (Figure 1) at the depth of 90 metres. The PLM is a highly suitable structure for testing drone’s inspection capabilities. It also includes a dummy ROV panel with marking for intervention scenarios. Further in 2018 and 2022, a Subsea Docking Station (SDS) and an instrument rig were installed at location C (Figure 1) at the depth of 365 metres. The SDS represents a testbed for docking and residency while the instrument rig enhances the situational awareness (Figure 2). The instrument rig delivers real-time visual and acoustic observation of the SDS, as well as environmental data such as currents, salinity and temperature at the site (Figure 3). The shoreside control room (Figure 5) is located at Trondheim Biological Station (location A, Figure 1) and is connected to both subsea locations with umbilical that provides power and data linkages. This setup offers a unique possibility to conduct full-scale testing and validation.
Offshore inspection and intervention operations with remotely operated vehicles (ROVs) and support vessels entail large costs and significant greenhouse gas emissions. Particular attention is paid lately to resident underwater drones that can be operated from land at their offshore installations. Resident UID is an autonomous vehicle deployed in the ocean for extended periods of time, operating reliably in uncertain environmental conditions and executing a variety of inspection or/and intervention tasks. Upon task completion it returns to one of the nearby SDSs for wireless charging and data transfer. The UID uploads the data collected and downloads new tasks or mission plans.
Equinor 3-modal communication concept for UIDs, inductive (yellow), optical (blue), and acoustic (green). Image courtesy of Equinor.
UID qualification for offshore deployment
In order to qualify a UID vehicle for deployment at the Johan Sverdrup oil and gas field, a dedicated programme divided into different sections was established: launch and recovery, basic to advanced level manoeuvring, docking and residency, inspection, intervention, endurance and communication. This was an opportunity for Equinor to test the SDSs before their offshore installation, as well as the 3-modal communication concept they promote for offshore resident vehicle applications (Figure 5). The design of the 3-modal communication concept assumes that vehicle uses inductive connection for high-speed data transfer (80Mbps – 1Gbps) while docked on SDS, medium bandwidth optical link (up to 10Mbps) in the vicinity of SDS (up to 50 metres) and low-bandwidth, long-range acoustic link that covers the whole operational area.
Through this qualification programme, OceanLab has demonstrated its flexibility to adapt to different testing requirements. The Johan Sverdrup SDS and communication tower with the optical modem were installed next to the existing PLM module at site B. This PLM-SDS-tower setup (Figure 6) has supported the 3-modal communication concept and provided infrastructure for qualification of manoeuvring, inspection, intervention, and subsea docking abilities (Figure 7). Furthermore, a secondary SDS dedicated for the Åsgard field with a communication tower was installed at site C at 365 metres depth. Assets at both sites B and C were accessible and operated from the shoreside control room. The OceanLab, i.e. sites A, B and C created realistic offshore environment in which vehicles could fly from one SDS to another (from 90 to/from 360 metres) using the suitable communication modality depending on their position relative to SDS and perform a variety of manoeuvring, inspection and intervention tasks. The testbed installation phase took place from June to September 2021 while qualification was done in September and October 2021.
Further development
The 3-modal concept will be implemented on both test sites B and C. The latter closely replicates offshore setup and is dedicated to work-class vehicles that have the potential to become resident drones on offshore installation. From 2022/2023, site B will consist of fully equipped docking station for observation-class vehicles, as well as structures for inspection and intervention. Both sites are operated from the OceanLab control room. Apart from subsea installations, control room supports access to other remote assets via various wireless communication systems, located e.g. on Svalbard. It allows remote operations and experimentation with the minimum or no crew in the field.
Ocean Space Centre
Through the Ocean Space Centre development in Trondheim, the OceanLab will be developed in all domains to improve the opportunities for field trials and experiments. To support subsea operations, the pier will be extended to include 1000 m2 of rigging area together with a 600 m2 workshop and maintenance building. Construction is expected to start in 2023. The facility will be connected to the test tanks and laboratories on the main Ocean Space Centre campus at Tyholt to facilitate hybrid testing.
Conclusion
The OceanLab has demonstrated its functionality and flexibility through an Equinor UID qualification programme and proved to be a valuable asset for development, testing and validation of autonomous and remotely operated vehicles for inspection, intervention and docking/residency tasks. Equinor, the Research Council of Norway and NTNU invested significant funds and effort into the infrastructure that is available now and welcome partners from industry and academia.