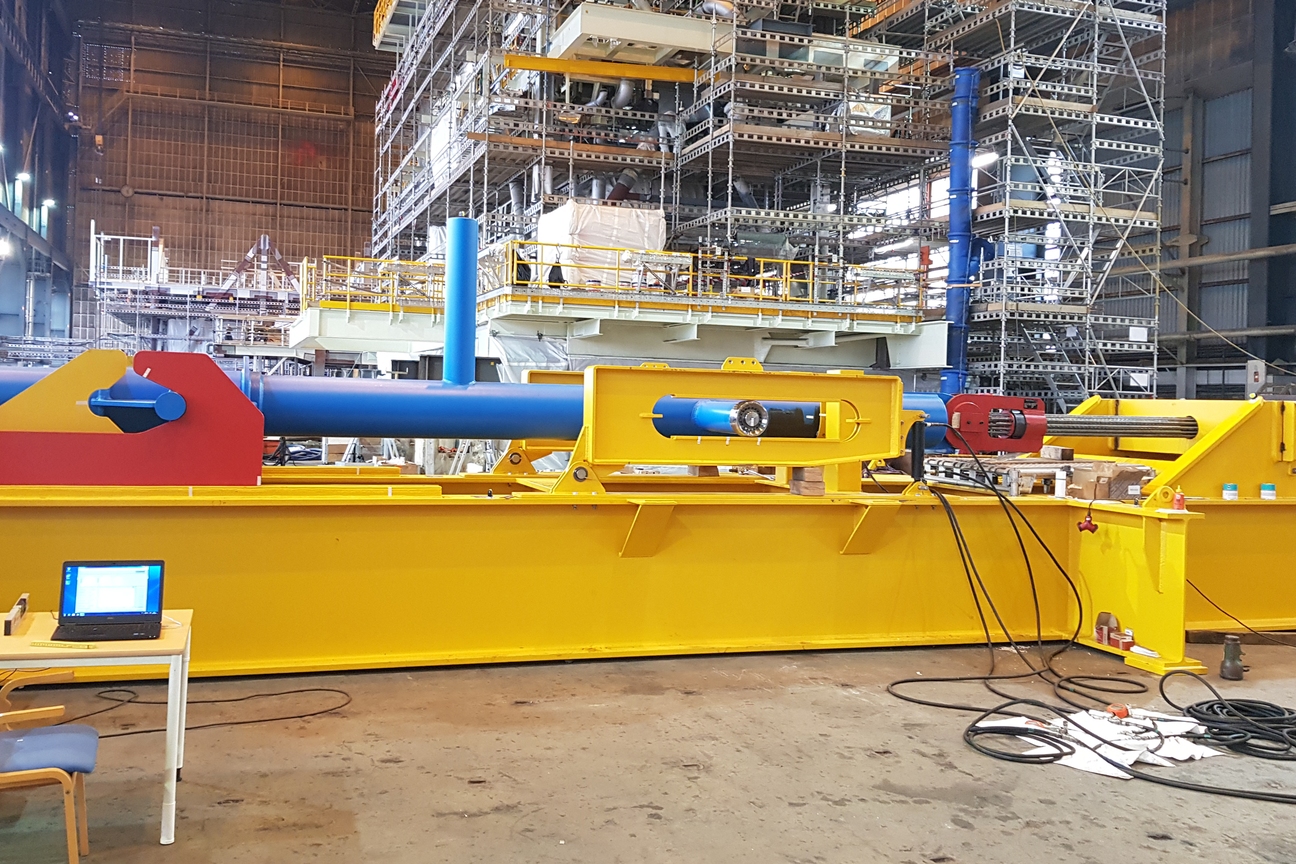
Subsea-studier og prototyper på Rosenberg
Noen av ingeniørene på Rosenberg har de siste årene fått den spennende muligheten å jobbe med utvikling av nye Subsea-løsninger for Equinor. Dette har foregått i regi av en rammeavtale som primært handler om videreutvikling av Equinors CAP-X konsept. Dette har også åpnet for samarbeid med andre aktører i bransjen, som blant annet Baker Hughes og Halliburton.
I utviklingen av nye løsninger er kunnskapen vi har fra fabrikasjonskontrakter og nærheten til fabrikasjonshallene viktig. Det er dette som danner bakgrunnen for begrepet Ekte Engineering, som vi liker å si at vi driver med. Mer konkret så betyr det at vi på fabrikasjonsjobbene har observert og lært en del om at design noen ganger er unødvendig komplisert. Et eksempel kan være at måten fabrikasjonstoleranser blir anvendt på tegninger kan bli unødvendig komplisert. Og dermed drar man på seg et unødvendig høyt timeforbruk i fabrikasjonen ved at sammenstilling må utføres svært presist. Mens et mer slarkete og upresist design kan være enklere å bygge og allikevel fungere godt. I noen tilfeller kan man også bruke fabrikasjonsrekkefølge til å sikre at kritiske mål blir riktige på en enklere måte. Dette med å skape gode designløsninger er noe man aldri blir utlært på, og vi utfordrer ingeniørene våre kontinuerlig til å tenke funksjonalitet, enkelhet og praktiske, byggevennlige løsninger i sitt arbeid. Slik kunnskap er noe man typisk tilegner seg gjennom erfaring, og ikke lærer så mye om på skolen.
En av designoppgavene vi har jobbet en del med er hvordan man skal kunne klare å «levere» en manifold, sveist inn på en rørlinje som legges av et rørleggingsfartøy, i en posisjon på Subsea-rammen som er presis nok til å kunne utføre sammenkobling mellom manifold og juletre, og så låse manifolden i denne posisjonen. Her måtte vi se på både design av selve manifolden og et arrangement for å låse den fast i en presis posisjon. I en annen studie så vi for øvrig på design av choke bridge, koblingen mellom manifold og juletre, og hvordan denne kunne lages så fleksibel som mulig.
3D-modell av testriggen, inkludert «moment-maskin» og Strand Jack.
For manifold og festesystem var dette de viktigste forutsetningene og designoppgavene:
• Manifold vekt maks 15 tonn
• Rørleggingsfartøyet legger røret med manifold innenfor +0/-800mm i lengderetningen og med selve manifolden/røret rotert innenfor +/- 5 grader
• Om manifolden havner i verste posisjon og må flyttes til riktig posisjon, stritter røret i mot med opp til 1500 kN og 190 kNm (mot rotasjon)
• Endelig posisjon må være så presis som mulig
Etter å ha jobbet litt med dette og hatt noen gode diskusjoner med eksperter hos kunden kom vi frem til følgende prinsipper vi kunne jobbe videre med:
• Hydraulikk er velegnet til bruk Subsea og kan levere mye kraft. Helst temporære/ gjenbruk (tas opp etter installasjon) med enkel til- og frakobling
• For et enklere design er det ønskelig at hydraulikk og tilkoblet struktur jobber i en linje som er parallell med rørlinjen
• Hydraulikk og posisjoneringsutsyr bør helst sitte på Subsea-rammen, slik at manifolden ikke blir unødvendig tung på grunn av slikt utstyr
• Kanskje kan rotasjon av rør/manifold utføres ved hjelp av geometri
• Siden det er relativt store krefter kan det være greit stålstruktur bør belastes i strekk for å unngå å dimensjonere for knekking
• Et design basert på et kileprinsipp kan være egnet til låsing av manifold mot rammen
Tilslutt endte vi opp med et design som kunne virke. Her ville vi lage en trunnion tvers av røret (manifolden) – og manipulere orientering og posisjon ved å ta tak i denne. En mock-up variant av manifolden er blå på illustrasjonene.
For å ta tak i trunnionen designet vi noen lange trekkeører (røde) som er festet i et litt slarkete skinnesystem på undersiden og i hydraulikksylindre (grønne) i den ene enden.
Trekkeørene har en slik form at de vil fange trunnionene på manifolden når de beveger seg horisontalt – og også rotere manifolden til riktig orientering.
Manifolden vil så bli ført, ved hjelp av dette litt slarkete og upresise trekkearrangementet, inn i noen fastsveiste låseører (del av gul struktur), som er montert veldig presist. Dermed sikres det at manifolden havner i riktig posisjon. Posisjonen låses ved hjelp at et ROV-operert kilesystem, og hydraulikksylinderne fjernes.
Illustrasjonene her er av en prototype som ble designet for å teste om designet ville fungere som forventet, og «levere» manifolden i forventet posisjon.
Dimensjonene på prototypen er begrenset til et relevant utsnitt av en Subsea-ramme, og utsnittet ble bygget i full størrelse. I tillegg ble det brukt en Strand Jack (rød lengst til høyre) for å simulere rørlinjens motstand mot å bli flyttet og en «momentmaskin» ble brukt for å simulere motstand mot rotasjon.
Prototypetesten demonstrerte at denne løsningen fungerer, samt at noen forbedringspunkter ble identifisert. Planen fremover er at denne teknologien skal utvikles videre i et vanlig teknologikvalifiseringsløp. Og om det går hele veien, vil Subsea Hook-up spooler bli overflødige på de lokasjonene denne teknologien egner seg.